
However, the formulation of hard, monolithic, flexible coatings such as polyurea is now resolving this problem for contractors, engineers, and facility administrators. When applied directly to cement or metal surfaces, polyurea not only reinforces and protects the underlying substrate but can also bridge gaps and cracks.

Containment Requirements
Federal and state regulations mandate the use of primary and secondary containment systems to keep toxic or hazardous substances from escaping into the earth and potentially entering the water supply, whether at factories, industrial plants, or other manufacturing buildings.
This provision implores the understanding that primary containment is not infallible. Though durable, metals corrode, concrete cracks, and is porous, so it will drain fluids if uncoated. This requires secondary containment, which often takes the form of concrete pits with barriers installed around the perimeter of a tank or other storage container.
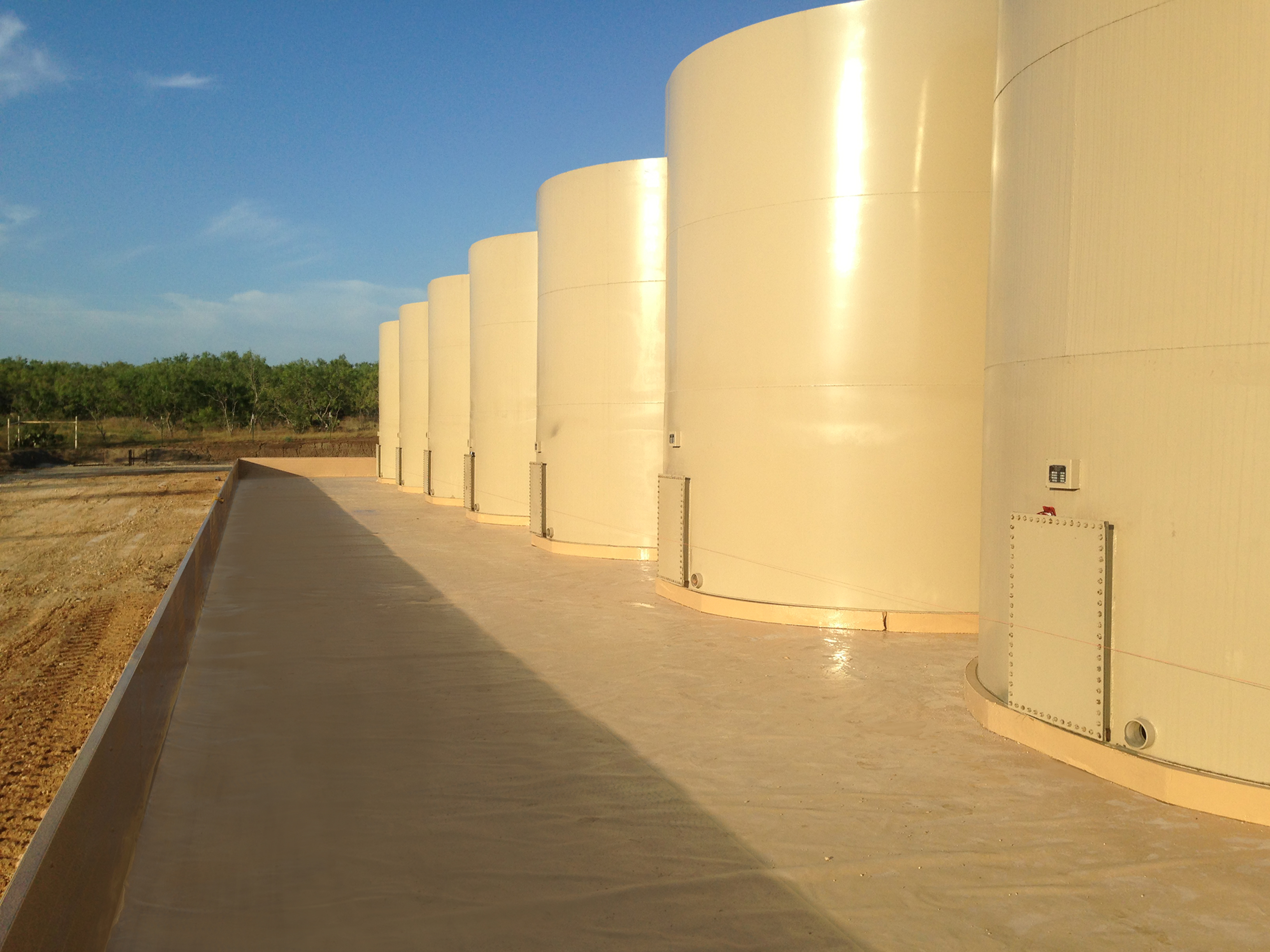
Typical coatings do not hold up well to substrate movement or daily, seasonal, or process-related thermal expansion and contraction, which can lead to cracks and leaks.
When applied to substrates such as cement or steel, the spray-applied waterproof coating creates a durable, seamless, elastic, protective barrier that prevents leaks and strengthens the integrity of primary and secondary containment systems. The coating exhibits superior physical properties such as hardness, tensile strength, as well as crack bridging and elongation up to 400%, to create a robust, industrial-grade protective covering.
While traditional coatings such as cementitious, epoxies, tars, and polyurethanes will precipitately fail if not installed under a comparatively narrow range of temperatures, polyurea is designed for installation and use from -40°F to +350°F. It sets and cures quickly and will withstand decades of freeze-thaw cycling, and wide variations of temperature and moisture.
Holds up to Extreme Weather

Want to learn more about Polyurea ?
Would you like to know how to get started as an applicator?
Head over to ArmorThane .com, they have been around for over 30 years and are the most trusted name in the business.
0 Comments:
Post a Comment
Note: Only a member of this blog may post a comment.